STORITVE
Akustična emisija
Akustična emisija
Neporušitveno preizkušanje – NDT
Neporušitveno preizkušanje (Non Destructive Testing ali NDT) je opredeljeno kot preizkušanje osnovnega materiala, delov materiala ali celotnih sistemov brez njihove oslabitve, kar omogoča nadaljnjo varno uporabo materiala ali sistema. Vzorec je neporušitveno testiran, če je po testu vrnjen v uporabo.
Namen NDT je raziskovati lastnosti materiala. NDT se uporablja za ugotavljanje sprememb v strukturi materiala, zaznavanje razpok ali drugih fizičnih nepravilnosti, za merjenje debeline materiala in plašča ali za določevanje drugih karakteristik industrijskih izdelkov.
NDT ni omejeno le na zaznavanje razpok, ampak tudi na zaznavanje drugih nepravilnosti, kot so poroznost, stanjšanje stene (npr. zaradi korozije) itd.
Ena izmed naprednih NDT metod je tudi akustična emisija (AE).
Akustična emisija – AE
»Materials “talk” when they are in trouble.«
Akustična emisija je fizikalni pojav – zvočno valovanje, ki se pojavi ob obremenitvi materiala (z obtežitvijo, nategom, dvigom tlaka …). Obremenjen material oddaja zvoke zaradi notranjih napetosti, razpok, trenja ali drugih fizikalnih procesov. Ti zvoki so običajno visokofrekvenčni in jih ni mogoče zaznati s prostim ušesom, zato se za njihovo detekcijo uporabljajo posebni senzorji s piezoelektričnimi kristali, ki pretvorijo visokofrekvenčne zvoke v električne signale. Signali nato potujejo preko posebnih koaksialnih kablov v napravo za zajem podatkov, ki beleži čas in intenzivnost zvočnih dogodkov. Zbrane podatke analiziramo, da ugotovimo vzorce, kot so frekvenca, amplituda in časovna razporeditev zvočnih dogodkov. Te informacije se nato uporabijo za razumevanje stanja materiala – prisotnost razpok, napetosti, korozije ali drugih strukturnih nepravilnosti.
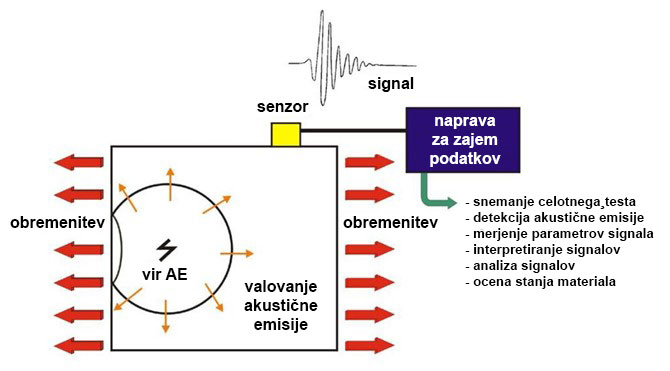
Skupaj ti koraki omogočajo uporabo akustične emisije kot orodja za neprekinjen nadzor, diagnozo in spremljanje stanja materialov in struktur v različnih industrijskih okoljih. Tako pomagajo pri preprečevanju nezgod in ohranjanju varnosti ter zanesljivosti materialov in struktur. Metoda akustične emisije se najpogosteje uporablja v petrokemijski, letalski, avtomobilski, gradbeni, energetski in geološki industriji.
Prednosti uporabe akustične emisije pri kontroli tlačnih posod
Preizkušanje z akustično emisijo predstavlja pomemben napredek na področju pregledovanja in preizkušanja opreme pod tlakom. Ker z AE zaznavamo samo aktivne defekte, z iskanjem in analizo statičnih defektov ne izgubljamo dragocenega časa. To pa posledično pomeni, da je oprema pod tlakom manj časa izven uporabe.
Druge prednosti akustične emisije so še:
- Medij lahko med preizkusom ostane v posodi → nižji stroški logistike, transporta in skladiščenja.
- Pregled z AE se lahko izvede celo, ko je oprema pod tlakom v obratovanju → nižji operativni stroški.
- Ni uporabe vode, posledično manjša možnost korozije znotraj posode → nižji stroški vzdrževanja, daljša življenjska doba opreme.
- Nižji preizkusni tlak → varnejši postopek pregleda.
- V relativno kratkem času se preveri celotna površina posode → hitrejša metoda.
- Zgodnje odkrivanje aktivnih poškodb → lažje načrtovanje vzdrževanja in popravil.
- Za pregled z AE se ne uporablja voda → bolj ekološko.
- Z AE se natančno določi lokacijo napake na posodi → natančnejši in zanesljivejši rezultati testov.
- Senzorjev ni treba namestiti neposredno na področje defekta → AE omogoča preizkušanje področij, ki so drugim metodam nedostopna.
- Z AE se zaznajo napake, ki se z drugimi NDT metodami ne (puščanje).
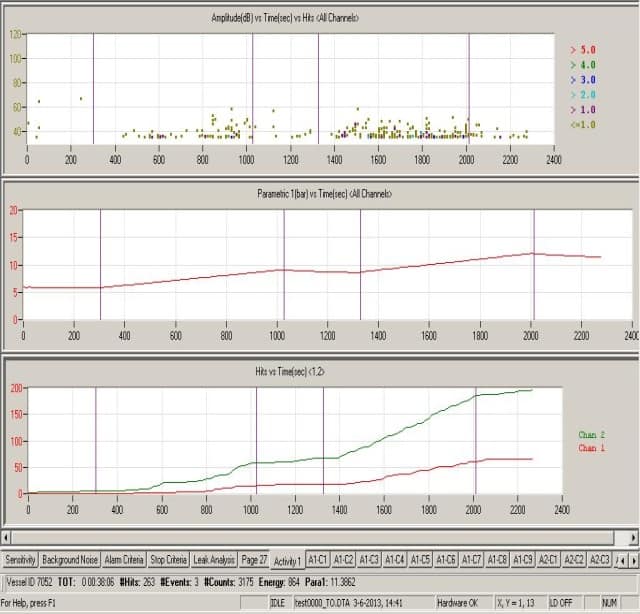
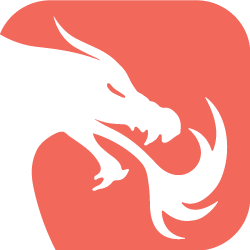
Druge naše storitve
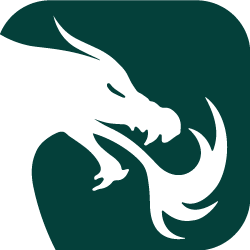